Keeping track of your keys, phone, wallet, or purse is a struggle for many people. Frantic searches of couch cushions and car seats are rarely successful, aside from finding the occasional candy wrapper, sticky penny, or lost coffee club card. Now imagine tracking millions of cannabis transactions every day, down to the gram. As part of the legal, regulated cannabis industry, this is your reality. All states permitting legal cannabis sales require adherence to state-based seed to sale marijuana software to track the location and sales of cannabis products in real-time. A few cannabis software companies fulfill this need, and metrc leads the way. It’s a software platform that requires scrupulous attention to detail for tracing cannabis plants and products through the supply chain. To date, metrc claims to have tracked over one billion events, making it “the most successfully-deployed regulatory cannabis system in the world.” For cannabis professionals, it’s critically important to understand what metrc is and what it’s not. This guide provides a brief overview of metrc, including links to metrc training videos.
Metrc stands for Marijuana Enforcement Tracking Reporting and Compliance. Headquartered in Lakeland, Florida, its cannabis software platform is currently required in Alaska, California, Colorado, Louisiana, Maine, Massachusetts, Maryland, Michigan, Missouri, Montana, Nevada, Ohio, Oklahoma, Oregon, West Virginia, and Washington D.C. Metrc enables tracking cannabis flower and products for all required reporting events in real-time for all license types. Metrc is a reporting system designed for government regulators; it is not a data analytics, CRM, or a POS management platform. That’s one reason you need a company like BLAZE and our partners to better manage and integrate with the metrc platform.
“Governments must balance public health and safety with the business needs of the regulated community” ⎼ metrc
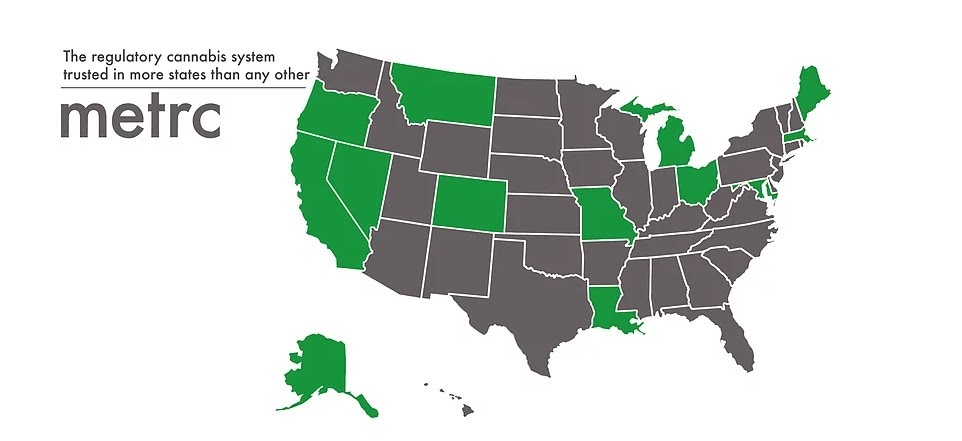
The core of metrc’s track and trace system is its unique identifier tags (UID) using Radio Frequency Identification (RFID). Metrc’s RFID system consists of three primary components:
- Hardware (Reader and Antenna)
- RFID Tag
- Software for both web and mobile applications
The low power RFID tags have a read range of 10 feet or more and do not require line of sight transmissions, meaning you can read tags through walls, doors, etc. Metrc claims that its tags are 8 to 10 times faster than barcodes with greater accuracy, faster compliance, and a search and find feature.
After a company orders and receives a set of tags from metrc, they’re assigned to two types of inventory; plants and packaging. Plants are placed in two categories, immature or flowering, and the tags remain connected to the plants until harvesting. All plants must enter the system through immature plant lots of up to 100 plants per lot and assigned a UID tag (typically a sticker) for the entire lot. Individual flowering plants are then given a plant a tag placed around the stem at the base. In the software, the operator updates the “Change Growth Phase” option to set up the transfer from immature to flowering. The cultivator enters the number of plants being moved from the immature batch to the flowering phase, and must also include the designated room for the transfer. Again, metrc is a real-time system and if regulators conduct an onsite audit, the location data must match the plant’s physical location.
Metrc’s goal is error-free tracing throughout the plant and product lifecycle, often referred to as the “chain of custody” with its single-use UID tags. If an error is made when assigning a tag to a plant, that plant’s tag needs to be replaced using the “Replace Tag” option in metric’s software. If an error is made when assigning a tag to a package, the package quantity in the package in question would need to be adjusted to “0” with “Entry Error” cited as the reason for the adjustment. That plant tag (or package tag) should then be finished in the system, replaced with a new, correct tag.
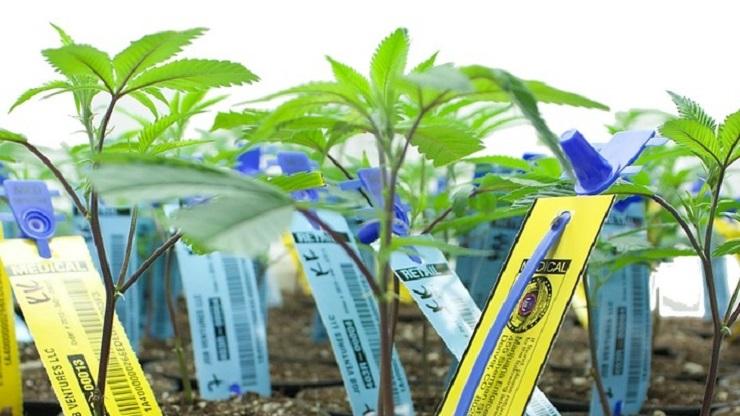
When it’s time to harvest, metrc requires compiling a “Harvest Batch” for the cannabis harvested in a single day. Metrc defines harvesting as cutting the entire plant and moving to a different, designated location for drying and curing. To create a Harvest Batch in metrc, the operator enters the plants’ original UIDs and creates a new Harvest Batch for this stage in the chain of custody. Metrc requires unique names for each Harvest Batch, and as a minimum best practice, using the strain name and harvest date to identify the Harvest Batch. Data input required includes:
- Weight. The plant in its entirety after being cut from the root ball including the stems, stalk, flower, leaves, trim, etc.
- Waste. Metrc permits multiple entries for bio waste but they must be reported within three days after the waste is created. Waste may include stems, stalk, flower, leaf, trim, etc.
- Package. A package with a unique identifier (flower, leaf, kief, fresh cannabis plant, or pre-rolls).
- Finish. A “Harvest Batch” is finalized when the cultivator divides the flower into packages and calculates all the waste.
- Transfer. To move the completed Harvest Batch, the cultivator must create a “Transfer Manifest” to move the product (by a licensed distributor) to a processor or manufacturer, or to a distributor for testing and quality assurance prior to retail sale.
Packages, Intermediate Batches, Production Batches, and Transfers
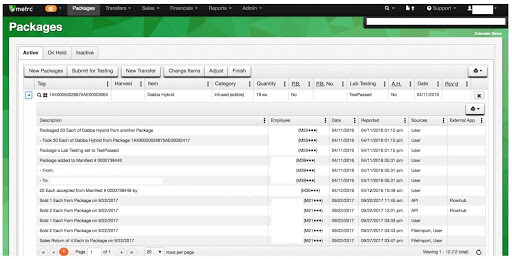
Packages can also be created from immature plants, Harvest Batches, testing lab samples, Production Batches, and other packages. Any amount of cannabis or cannabis product that may be sold, manufactured or transferred, must be placed into one or more packages, each package having a UID (package tag) created in metrc. Any product that a company intends to transfer from one licensee to another must have a UID which must be physically attached to the package. Fortunately, metrc allows you to repack any package into a new package, just ensure this step occurs and the data is entered correctly for accurate tracing.
Packages can be used to create an Intermediate Batch such as making a concentrate product. Existing UIDs can be entered to create an Intermediate Batch to create a new package for the concentrate. The newly packaged concentrate may then be partially used in a Production Batch to make an infused product such as an infused edible or infused non-edible, or another concentrate.
A Transfer Manifest must be created anytime a package moves from one licensed facility to another, even if it’s on the same property. It shouldn’t come as a surprise that metrc requires transporters to record their actual departure and arrival times. Once received, if a company receives a package that doesn’t match the weight, volume, or count on the manifest, they must adjust the package in their inventory to report the actual, adjusted weight, volume, or count. A transfer can be rejected by individual packages within the shipment, or wholly reject all packages. A rejected package requires the originating licensee to receive the rejected package back into inventory.
Transfers to Another Licensee
To move a package to another licensee, the company must also create a Transfer Manifest within metrc. Required data includes planned route information, the name of the company conducting the transfer, driver name, and the vehicle information. At least two copies of the Transfer Manifests must be printed, and the driver must carry a printed version of the Transfer Manifest at all times.
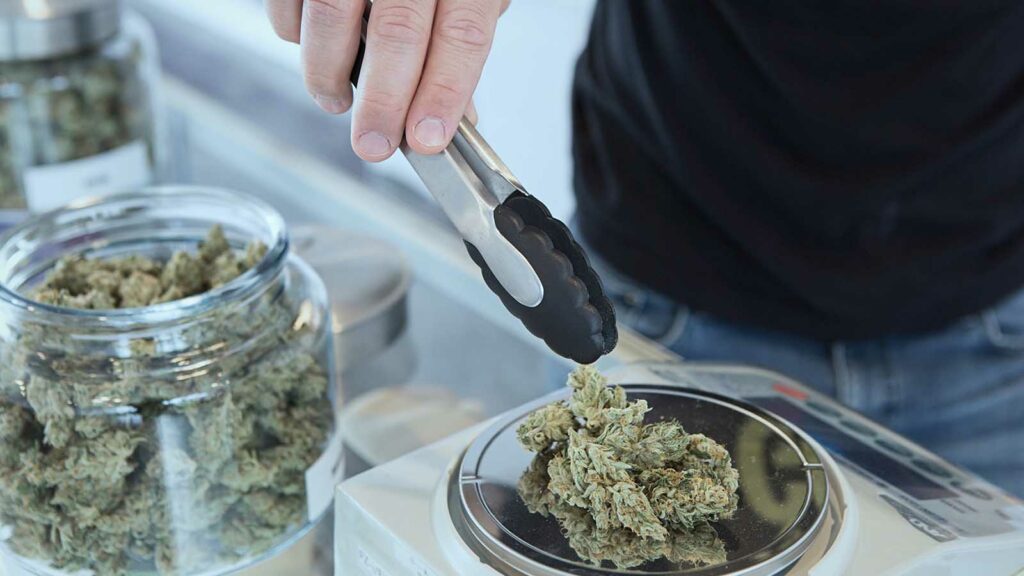
Final Retail Sales
Recording sales in metrc is the last reporting event in the chain of custody. Each sales transaction must be entered into metrc, and while details may differ from state to state, data typically includes:
- Total quantity and the unit of measure.
- Date and time.
- The total sale amount in dollars.
Retail sales transactions must be entered into metrc within 24 hours, so it’s best to develop an SOP for doing so. This is where BLAZE Retail plays an important role and our seamless integration with metrc, because:
- All sales are synced.
- Transactions are uploaded in real-time to avoid potential errors with batch processing.
- Refunds are synced in real-time.
Help and Training
Metrc provides a support desk as a resource for the industry and the state regulators. They also provide troubleshooting and guidance on hardware and software through a dedicated support team approach, a toll-free number, and email communications. Training is also a key component of the metrc support program. Their YouTube channel has several short video tutorials to help acquaint yourself with the metrc system.
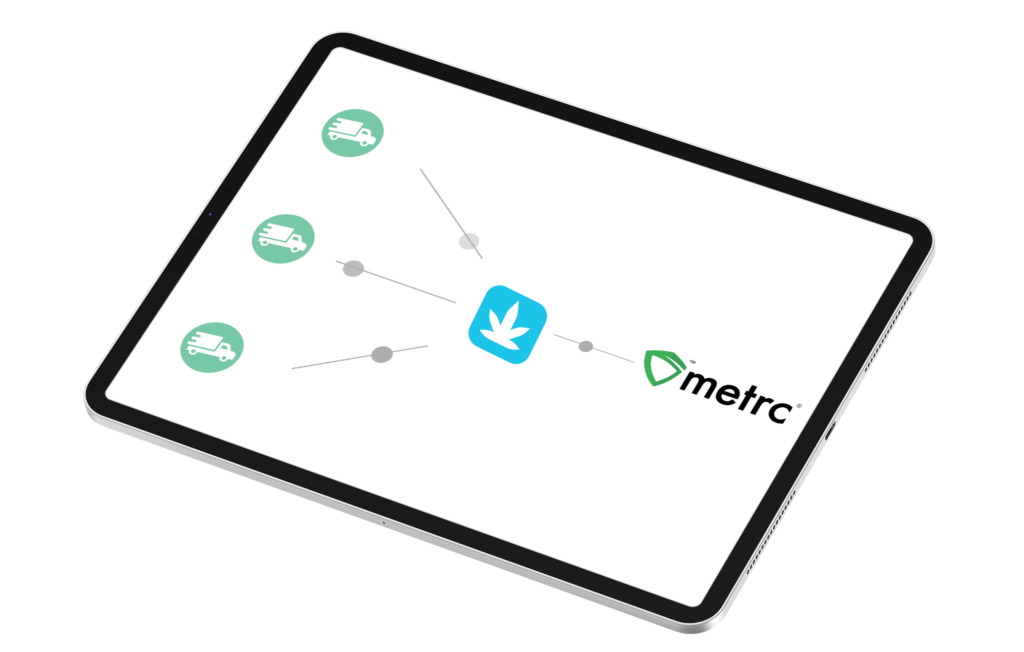
BLAZE + Metrc
We support metrc across our entire software suite to facilitate and simplify a secure chain of custody throughout the product’s lifecycle. Cultivators, distributors, dispensaries, and delivery partners can all benefit from our metrc experience and our relationship with them. Let us show you how! Book a demo or contact us today. We’re looking forward to it!